The Future of Maintenance: How Data is Revolutionizing Industry Standards
The industrial world is undergoing a seismic shift from the reactive, wait-until-it-breaks maintenance model to a proactive, data-driven approach. This evolution, known as predictive maintenance, is not just a change in repair tactics; it’s a fundamental transformation in how we view and interact with machinery.
Welcome to the era where data doesn’t just support decisions; it drives the entire maintenance narrative. This is not just an advancement; it’s a complete cultural shift in maintenance and production forecasting. Here’s how data is not just changing but revolutionizing industry standards.
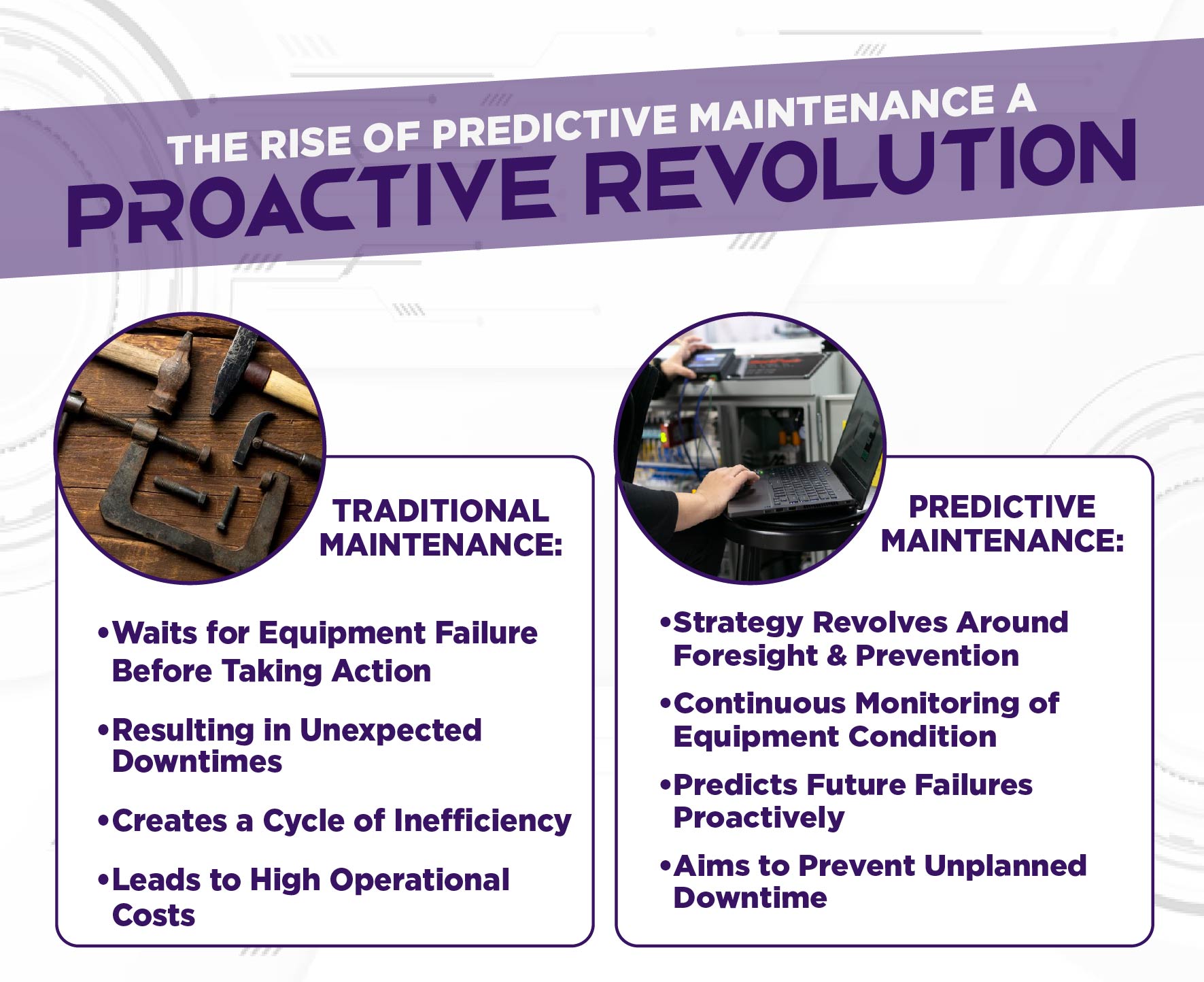
The Rise of Predictive Maintenance: A Proactive Revolution
Predictive Maintenance Unpacked
Predictive maintenance isn’t just about fixing issues before they become problems; it’s about understanding and preempting them.
By leveraging data analysis tools and techniques, it predicts equipment failures, allowing businesses to undertake maintenance at the most reasonable time. This not only significantly cuts down unplanned downtime but also extends the lifespan of machinery, enhancing overall productivity.
The Paradigm Shift from Traditional to Predictive
- Traditional Maintenance: Charact0erized by a reactive posture, this approach waits for equipment to fail before taking action. The result is often unexpected downtimes, rushed repairs, and a cycle of inefficiency and high costs.
- Predictive Maintenance: This strategy involves foresight and prevention. By continuously monitoring equipment condition and predicting future failures, businesses can plan maintenance activities more effectively and avoid the pitfalls of unplanned downtime.
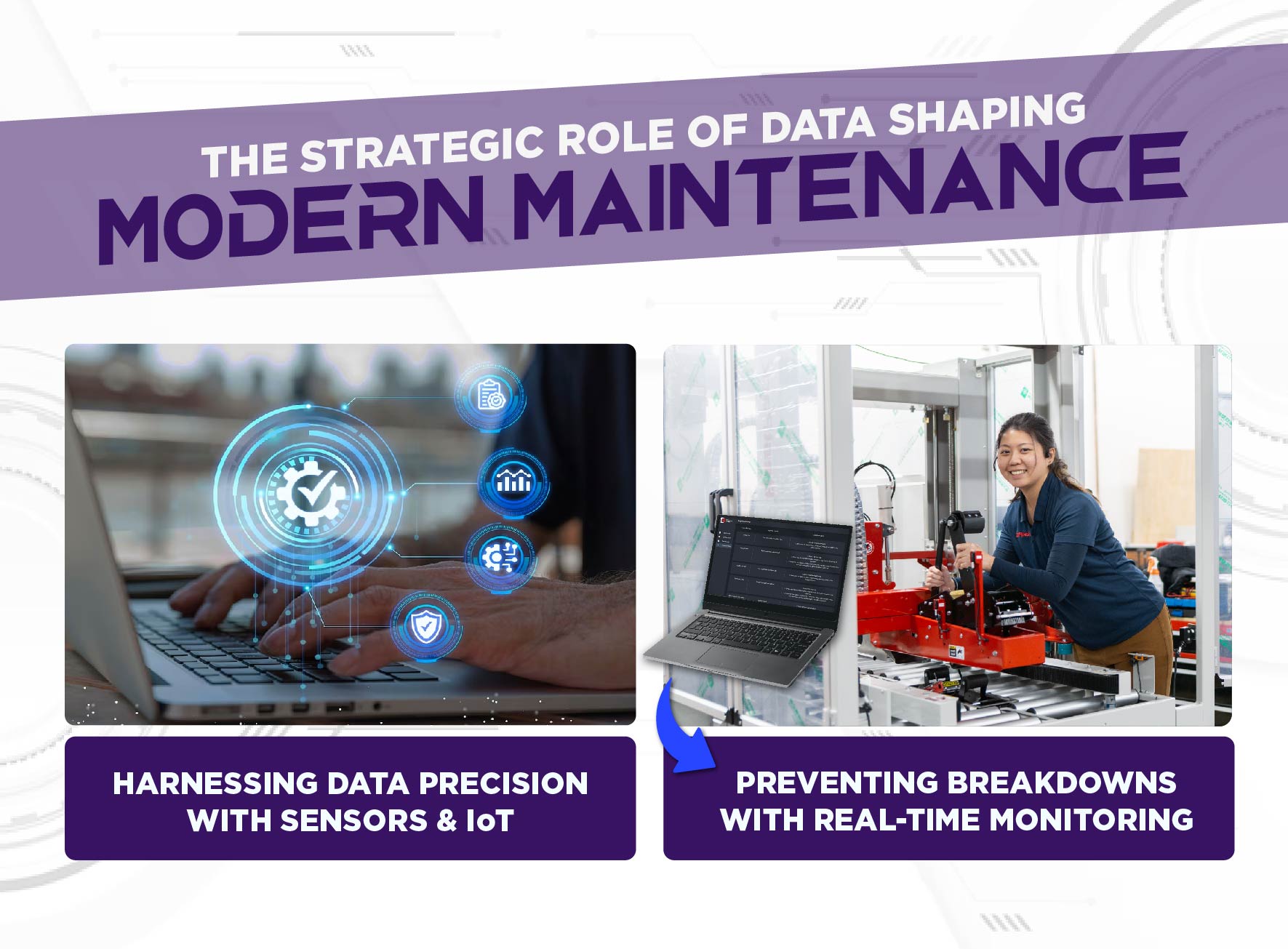
The Strategic Role of Data in Shaping Modern Maintenance
Data is the lifeblood of predictive maintenance. It’s the tool that turns guesswork into strategy, transforming how businesses approach machinery upkeep.
The Vanguard of Data Collection: Sensors and IoT
Machinery today is outfitted with an array of sensors, each meticulously collecting data points from operational temperature to vibration frequencies. When paired with the Internet of Things (IoT), these sensors provide a real-time data stream that is both rich and actionable.
This network of sensors and data points acts as the eyes and ears of the predictive maintenance strategy, providing the essential information needed for informed decision-making.
Real-Time Monitoring: The Pulse of Predictive Maintenance
- Immediate Anomaly Detection: With live tracking, anomalies are flagged as they occur, prompting immediate attention. This swift response capability is crucial in preventing minor issues from escalating into major breakdowns.
- Case Studies in Success: Numerous industries, from automotive to energy, have stories of how real-time monitoring and predictive maintenance have saved them from costly downtime and repairs, underscoring the value and effectiveness of this approach.
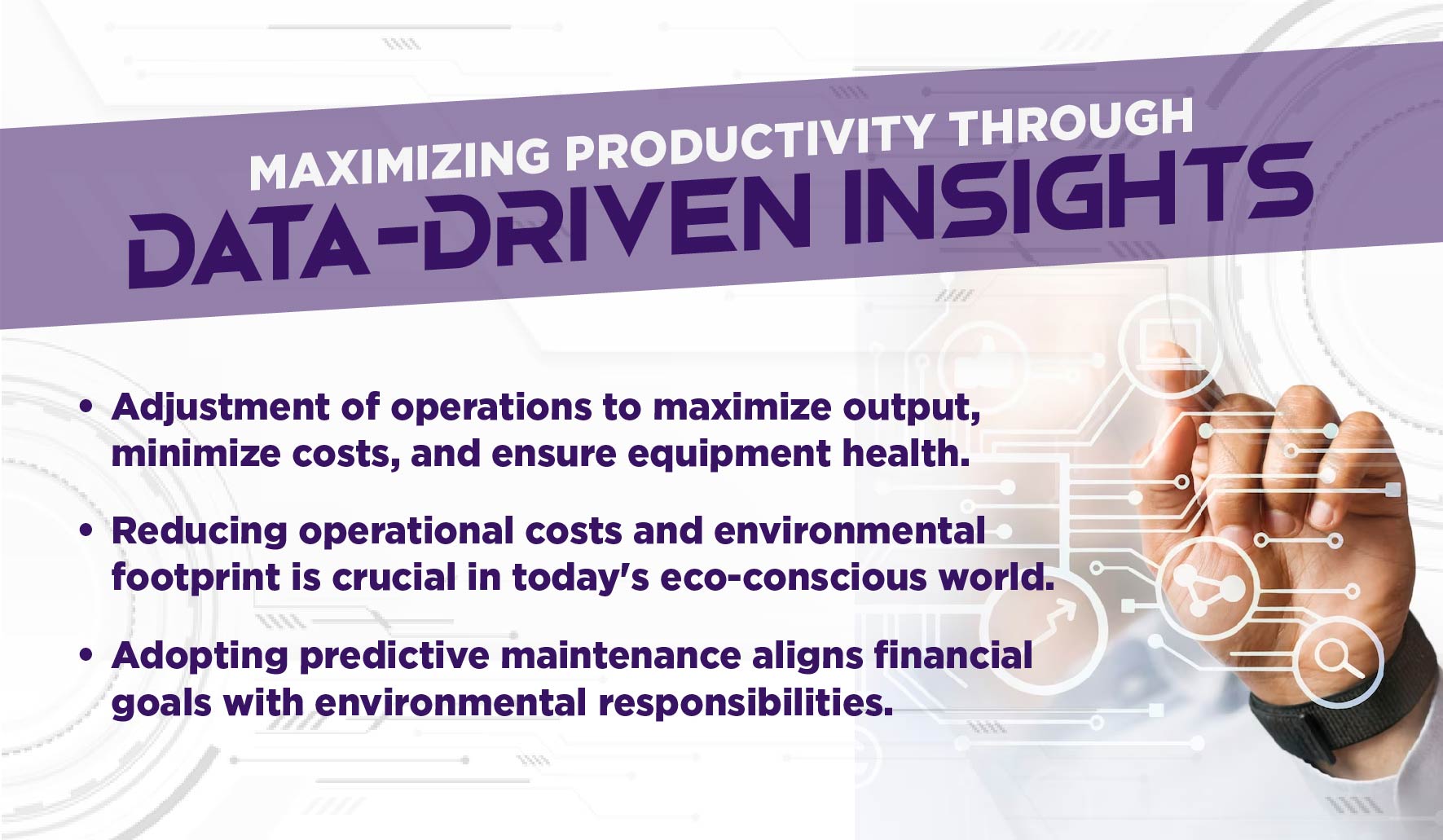
Maximizing Productivity Through Data-Driven Insights
In the fiercely competitive industrial landscape, maximizing machine productivity is not just an objective; it’s a necessity.
Fine-Tuning Operations for Peak Performance
Data doesn’t just predict failures; it provides a roadmap for operational excellence. Businesses can fine-tune their machinery for optimal performance by analyzing patterns and performance metrics. This means adjusting operations to achieve the highest output at the lowest cost, all while maintaining the health and longevity of the equipment.
The Symbiosis of Efficiency and Sustainability
- The Efficiency Edge: Through predictive maintenance, businesses can balance peak performance and minimal resource usage. This reduces operational costs and decreases the environmental footprint, a critical consideration in today’s eco-conscious world.
- Economic and Environmental Handshake: Adopting predictive maintenance aligns a company’s financial goals with its environmental responsibilities. The result is a synergy where cost savings meet sustainable practices, creating a win-win scenario for businesses and the planet.
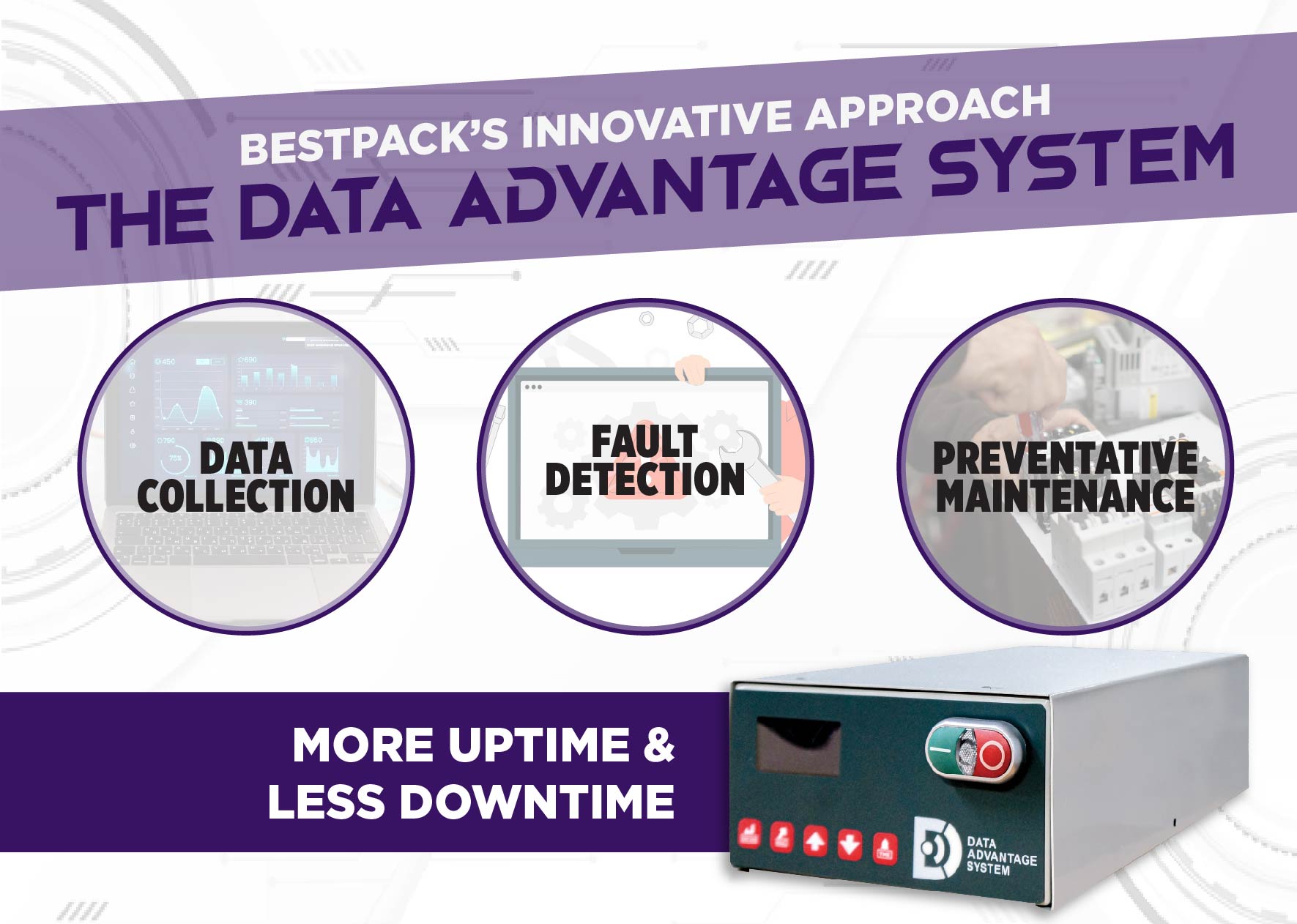
BestPack’s Innovative Approach
At BestPack, we’re not just participants in this shift towards data-driven maintenance; we’re pioneers. Our Data Advantage System (DAS) is a testament to our commitment to innovation and excellence in predictive maintenance.
The Data Advantage System (DAS)
- Data Collection: Our pre-mounted sensors don’t just observe; they capture crucial machine usage events, ensuring a constant stream of data. This data is then securely transmitted over WiFi and stored in the cloud for up to 3 years, providing an extensive history for analysis.
- Fault Detection: With DAS, fault detection is not just about identifying problems but understanding their root causes. By analyzing fault data, DAS pinpoints production issues, offering actionable insights for performance improvement and identifying machine failure rate anomalies to facilitate timely corrective action.
- Preventative Maintenance: The DAS doesn’t just alert you when things go wrong; it helps prevent issues from occurring in the first place. By providing weekly reports indicating when it’s time to service your machines, DAS ensures that your operations run smoothly and efficiently, reducing unexpected downtimes.
Empowering Operations with
- Remote Monitoring: In today’s globalized world, the ability to access real-time data from anywhere is invaluable. DAS offers this capability, reducing the need for local warehouse monitoring and empowering operators with instant access to critical data.
- Data Visualization: We understand that raw data can be overwhelming. That’s why DAS features a user-friendly and intuitive dashboard design, turning complex analytics into easy-to-understand visuals. This lets you make informed decisions quickly, backed by detailed and accurate charts.
Conclusion: Embracing the Future with BestPack
The future isn’t just coming; it’s here. Data-driven maintenance is setting new industry standards, and BestPack is at the helm of this revolution. With over 30 years of expertise and a commitment to innovation, we’re not just offering a product but a partnership in your journey towards operational excellence.
Ready to revolutionize your maintenance strategy? Explore how BestPack can transform your operations with our cutting-edge solutions. Connect with us today and step into the future of maintenance. Your journey toward predictive maintenance, enhanced productivity, and unparalleled operational efficiency starts here.